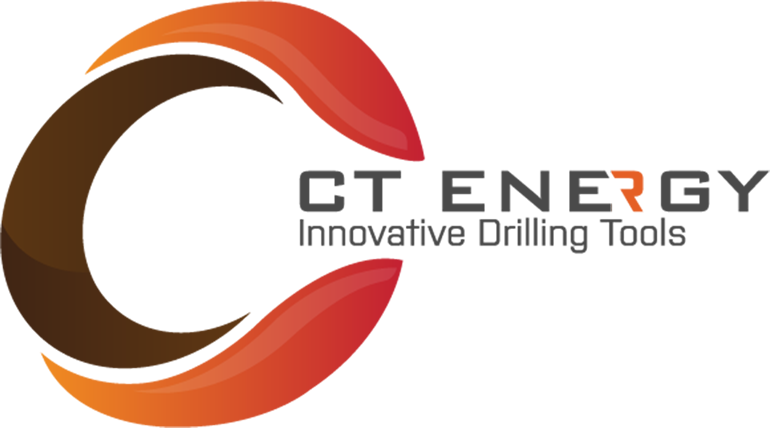
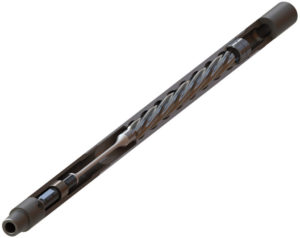
The Toe Tapper System
The Toe Tapper was developed through third party testing, taking the original negative pressure pulse design of the Ratler and what was achieved through our coiled tubing design to create a new patent. As a result, the Toe Tapper has proven to outperform the Ratler in both performance and durability.
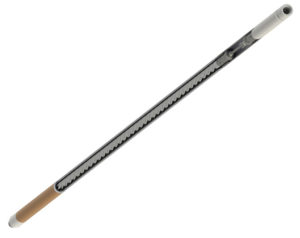
The HydroClutch
The HydroClutch employs conventional drilling technology with the addition of a specialized drilling-based motor system as a method of drilling horizontal wells. The revolutionary alternative to rotary steerable allows the operator to utilize the benefits of a conventional BHA while at the same time, capitalizing on the advantages of continuous drill string rotation.
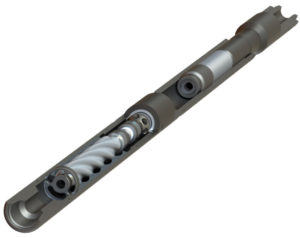
The Ratler
The Ratler is a downhole mechanical device that is used during drilling to reduce static friction and increase ROP. The axial vibration generated through a negative pressure pulse reduces drag and enables a more efficient transfer of weight onto bit.
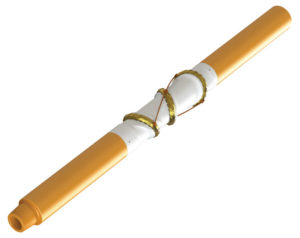
The Helix
The Ratler is a downhole mechanical device that is used during drilling to reduce static friction and increase ROP. The axial vibration generated through a negative pressure pulse reduces drag and enables a more efficient transfer of weight onto bit.
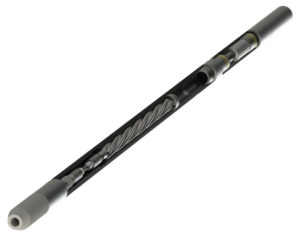
The Helix
The Ratler is a downhole mechanical device that is used during drilling to reduce static friction and increase ROP. The axial vibration generated through a negative pressure pulse reduces drag and enables a more efficient transfer of weight onto bit.
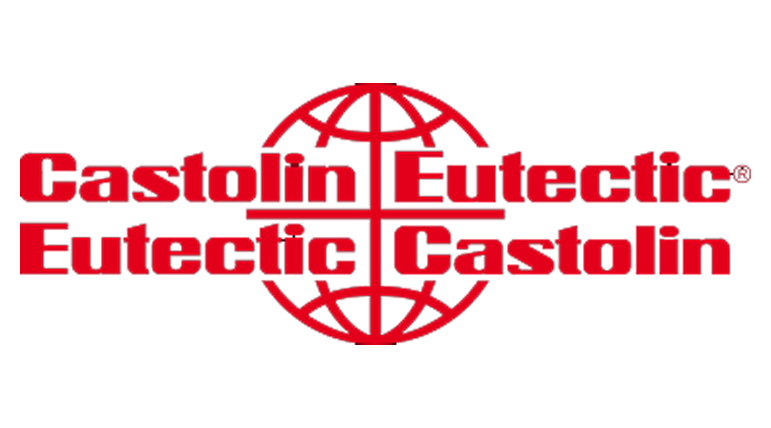
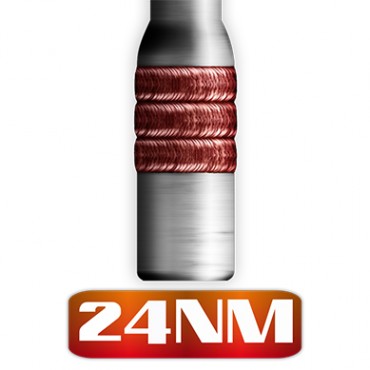
OTW 24NM
OTW 24NM
Castolin OTW 24NM is a, hard, stainless steel alloy, specially designed to protect non-mag drill collars, drill pipes and related components on the bottom hole assembly in drilling industry. The alloy is a gas shielded, metal cored alloy wire. The weld deposit is designed to give a crack-free, smooth surface with low friction properties. The wear life as welded will show about 3,5-5 times longer than the non-mag base material alloy, and for increased wear life in open hole environments may be dramatically increased by injection of tungsten carbide pellets into the alloy.
Specifically developed for new or worn non-magnetic hardbanding of wear bands applied on Non-magnetic drill collars and related drilling components. Designed to be applied on chromium-manganese, austenitic stainless steels and nitrogen bearing austenitic stainless steels. Commonly known base materials such as; P530, AG17, 1515LC NMS-100 and others.
OTW 24NM cored wire electrodes are precision wound on recyclable, red color plastic spools (EN ISO 544) to a standard weight of 15 kg and specially vacuum packed for optimum, storage protection. Bulk packaging is available upon request.
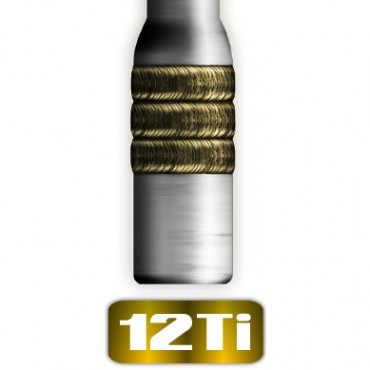
OTW 24NM
OTW 12Ti
OTW 12Ti actively prolongs against wear in the most extreme drilling conditions, as demonstrated by its performance in highly deviated well & open hole applications. Maximum drill pipe life is achieved through superior wear-resistant properties, coupled with the ultra-smooth, casing friendly features preferred by most oil companies.
OTW 12Ti Titanium-Carbide chemical composition creates a martensitic matrix, which infuses ultra-smooth / ultrafine compounds into an abrasion resistant, ultra-hard microstructure, ensuring optimal strength and metallurgicalintegrity.
OTW 12Ti hardness scale of 61.5 HRC, combined with our Non-Cracking (NCD) and Flexible Application Designs (FAD), enables high load, open hole performance while simultaneously meeting all casing friendly requirements. End-users yield a higher return on investment and long-term savings through OTW 12Ti‘s life-extending drill pipe technology.
OTW 12Ti can be reapplied over itself and most other hardbanding materials, ensuring quick and easy repair in even the most remote locations. OTW 12Ti is a flux-cored wire alloy, designed & manufactured by Castolin Eutectic in our own state-of-the-art facilities, of tool joints.
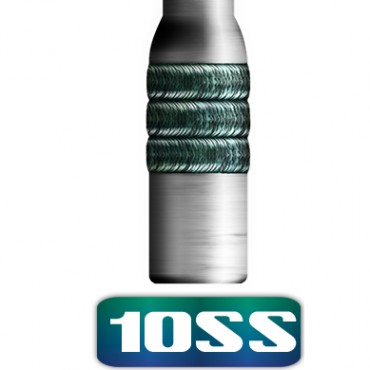
OTW 10SS
OTW 10SS
OTW 10SS is an exclusive gas shielded, metal cored alloy wire, specifi cally designed for use in severe sour (SS) environments and is fully compatible with all drill pipe sour service grades. Drill pipe sour service grades (VM 105 DP SS™, TSS™-105, CYX™-105) and HWDP differ greatly from normal API grades and use a modified form of steel on the pipe body and tool joints. This alloy is formulated to be non-cracking, easy to apply and repair, with low dilution and minimal pre-heat temperatures. The reduced overall hardness is designed to optimize performance in even the most severe sour environments.
OTW 10SS is formulated to produce a unique, hard tool-steel microstructure with numerous ultra-fine/ultra-hard phases, dispersed in a tough tempered martensitic matrix.
OTW 10SS produces an excellent, non-spatter bead in both appearance & quality, ensuring greater flexibility & increased arc stability between 100 to 400 AMP operating ranges”. Reducing labor costs, OTW 10SS offers a high deposition rate with exceptional, all-position welding ability. The result is a cost-effective solution for multi-purpose hardbanding applications, including Drill Pipe Tool Joints, HWDP Tool Joints & Center Wear Pads.
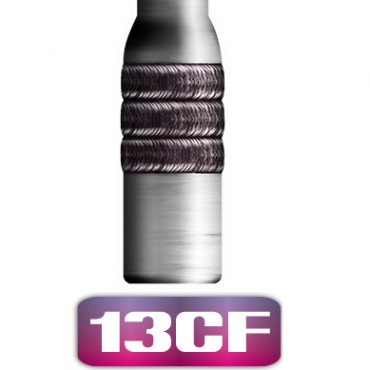
OTW 13CF
OTW 13CF
OTW-13CF has a Crack-Free Design, smooth surface with low friction properties and a microstructure designed to achieve a good balance between casing friendly and tool wear, whilst remaining a cost-effective solution.
OTW-13CF has a casing wear resistance that is superior to currently established Non-Cracking wires, whilst retaining a competitive level of all round tool wear resistance. It achieves this with a slag-free deposit that precipitates a dense dispersion of hard, primary niobium and complex CrMo carbide phases finely distributed in a martensitic/residual austenitic matrix. The good resistance to high stress abrasion and erosion even when combined with heavy impact or pressure, are typical conditions that can be expected in an open hole or cased hole environment. OTW-13CF is ideally suited to intermediate to advanced hardbanding applications.
OTW-13CF is an exclusive, gas shielded, metal cored alloy wire may be reapplied over itself to refurbish worn drill pipes after drilling operations and also any of the OTW range. The Flexible Application Designed (FAD) feature implies greater flexibility for the hardbander and significant cost savings in old hardbanding removal and pipe preparation.